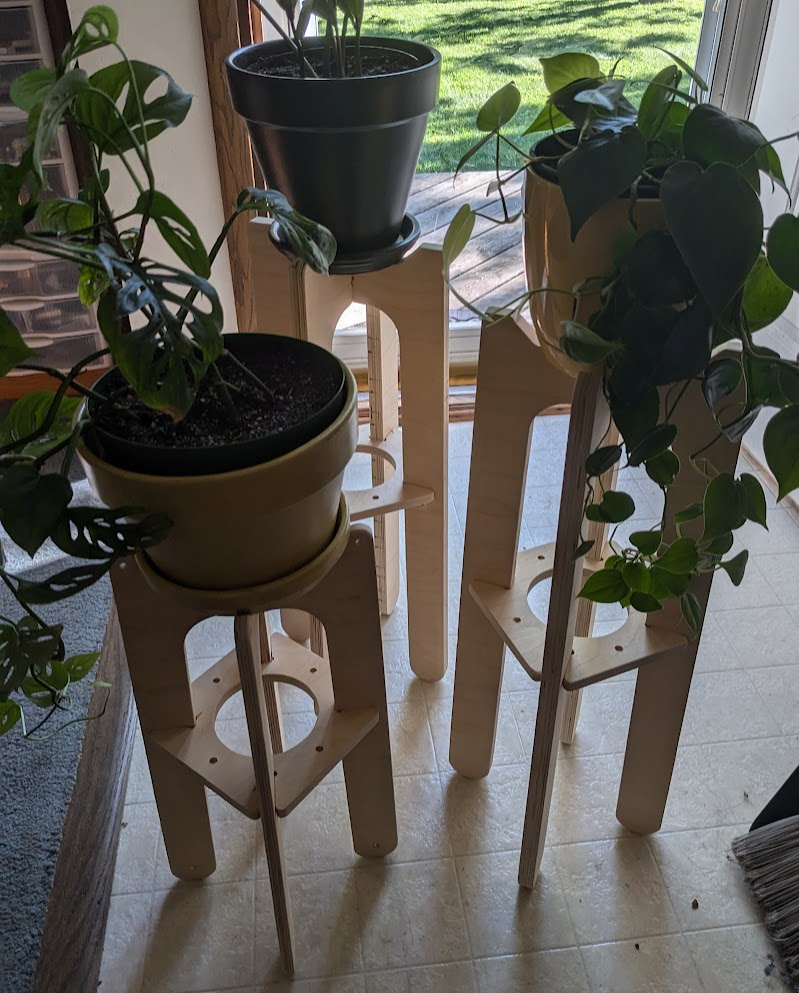
These stands are a project I did for my sister, who needed more space for plants in her apartment. After she asked, I took some measurements to get the right heights and make sure they could handle all of her pots then designed these for manufacture on a CNC router. Since these needed to be moved to her apartment, I designed them to be able to be easily taken apart and the parts to be stacked for easy transport.
Prototype
I knew that these stands were going to need a lot of material, so my first step was to make a small prototype to prove that the stands could fit the pots they were supposed to. My plywood supply was low at the time, so I made these prototypes out of thin polycarbonate that I had in excess. To be easily taken apart, I made the individual plates of the prototype to slide together nicely using slots and stay together by both friction and by a pot on top of the assembly pushing it together. If you are wondering, the weird little pockets on the bottom of the slots are to combat the fact that a CNC router can’t machine corners without rounding them. Without them, the bottoms of the slots wouldn’t lie nicely on each other.
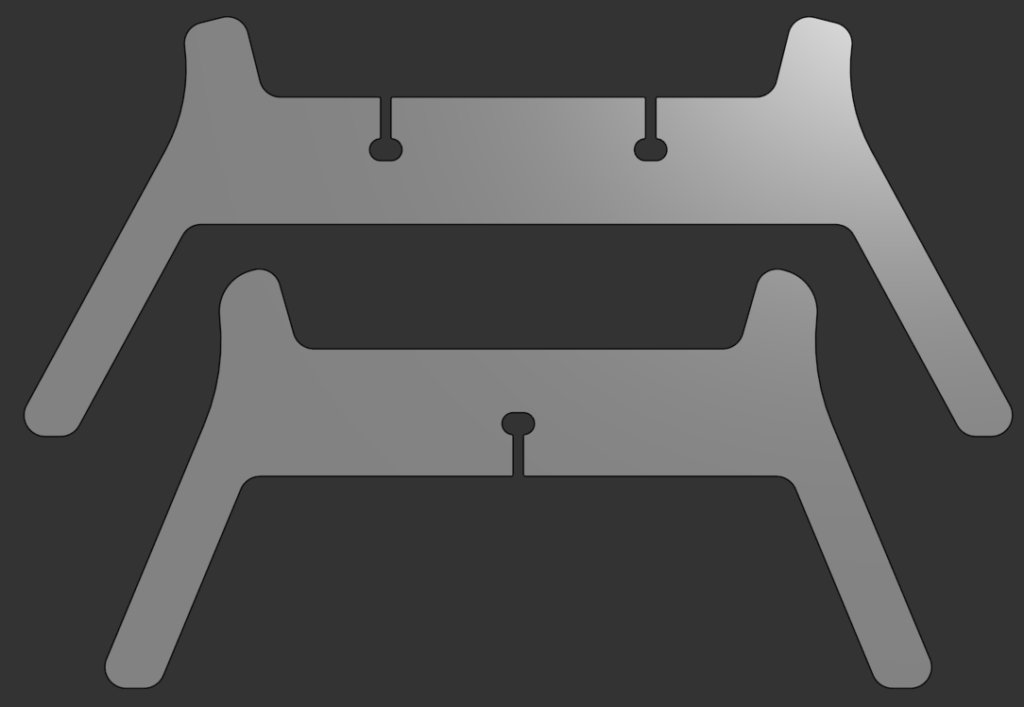
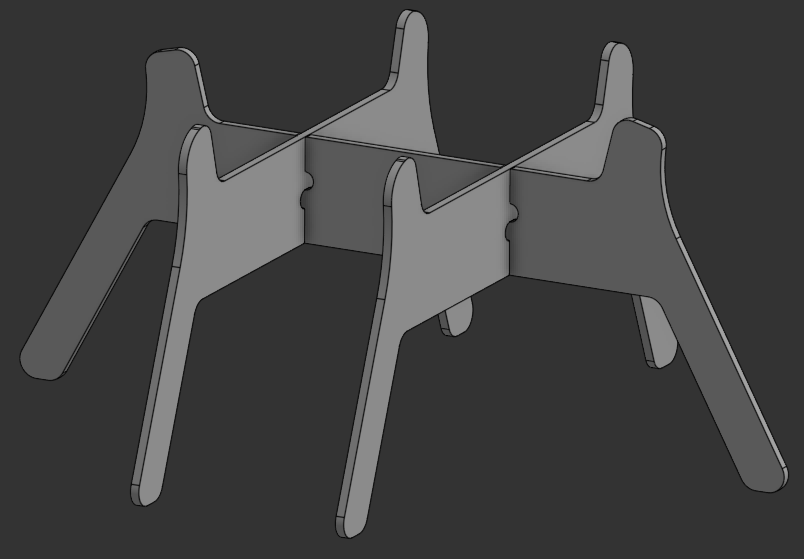
In action, the prototype worked decently well. Being polycarbonate, it did bend a little but that didn’t worry me too much since I knew that my sister wanted these stands to be made out of wood, which would be way stiffer. The pot in the image doesn’t really nestle into the holder as I wanted it to, but the ones that the final product would hold were larger and would behave better.
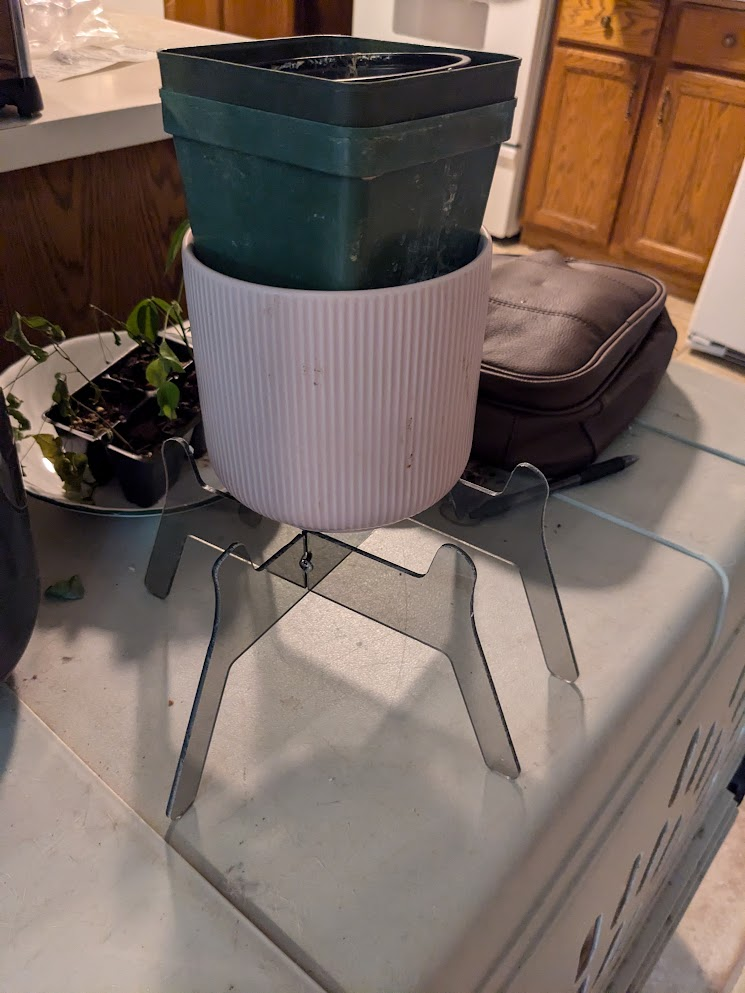
Designing the Final Holders
To start off the final design, I made a quick master sketch with the key parameters for holding the pots, holding them at a good height, and having a reasonably wide base for stability. My sister wanted the plants to be held up a couple feet, so I made them as tall as I could fit onto the plywood sheet I had available. This constraint of the available material also led me to a base of 10″, since said sheet was only about 30″ and I wanted to maximize the number of stands I could make on it.
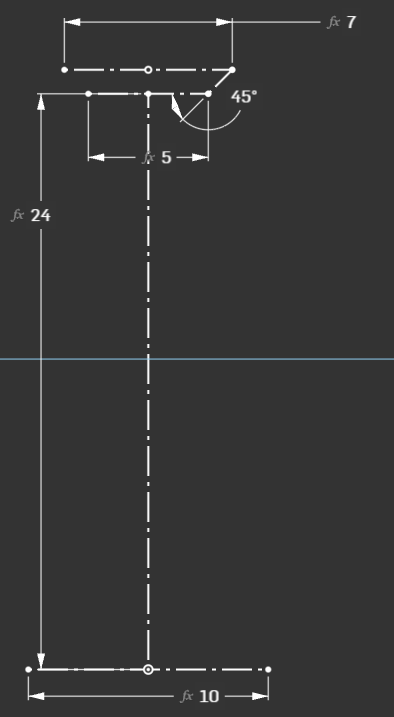
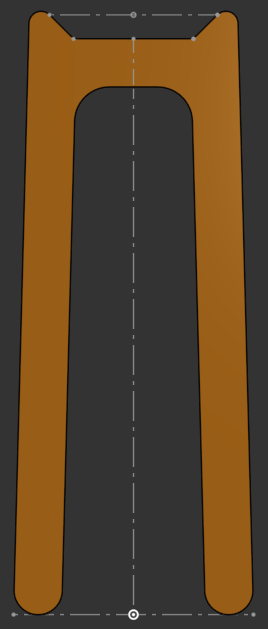
Given the stock constraints, I made sure that the shape of the stand legs allowed them to be nicely arranged for cutting. I made each stand from two halves rather than the 3 pieces of the prototype due to limited stock, as well as not needing as many points of contact. The polycarbonate was 1/8″ thick while the wood was 1/2″, so the pots have more surface area to rest on and are just as steady.
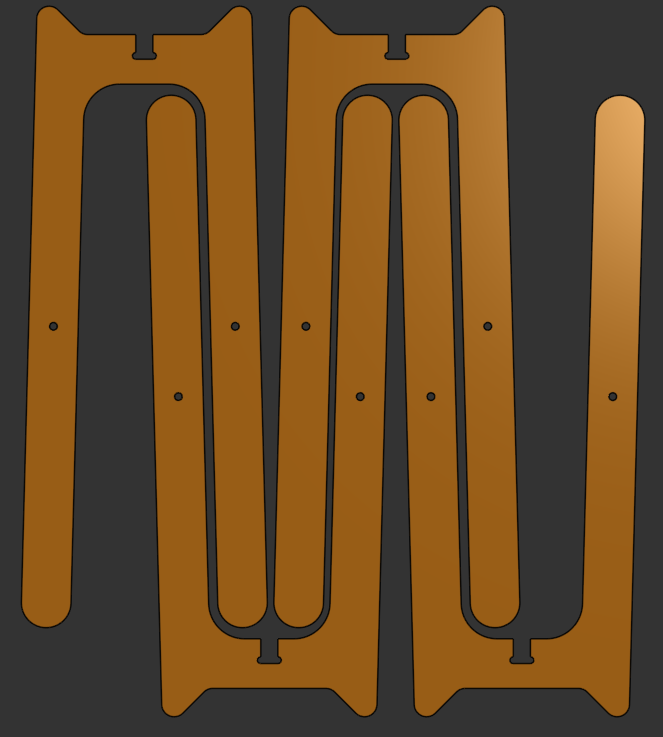
Put together, the new stands look considerably nicer than the prototype. An additional change I made for this version is that I added a brace in the middle of the legs, which helps with stability and staying together. By pushing it up it stretches the legs outward, which keeps it steady as well as keeping the assembly in one piece.
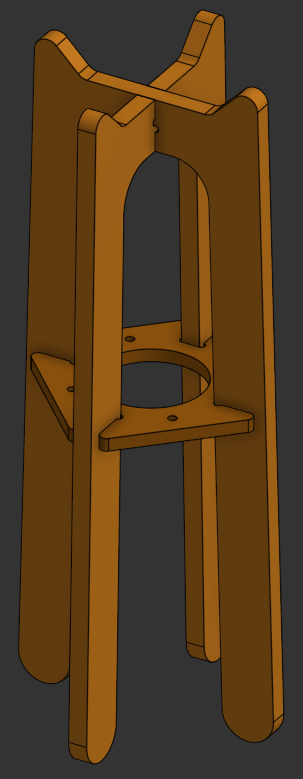
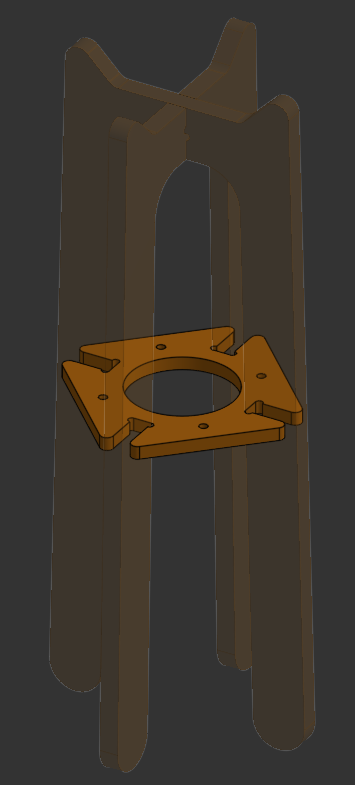
After showing my sister the design, she asked if I could also make a smaller one for variety. After making a scaled down copy, I was ready to group and manufacture all of my parts for three stands.
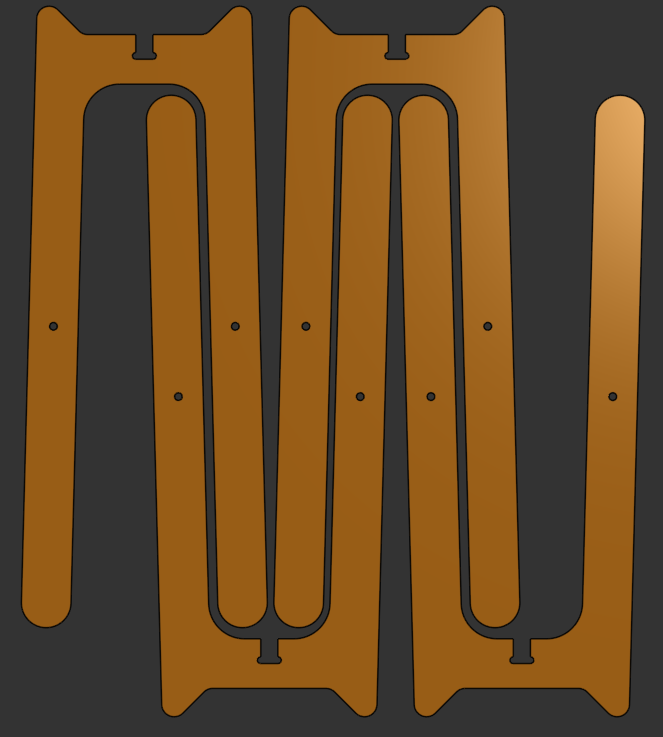
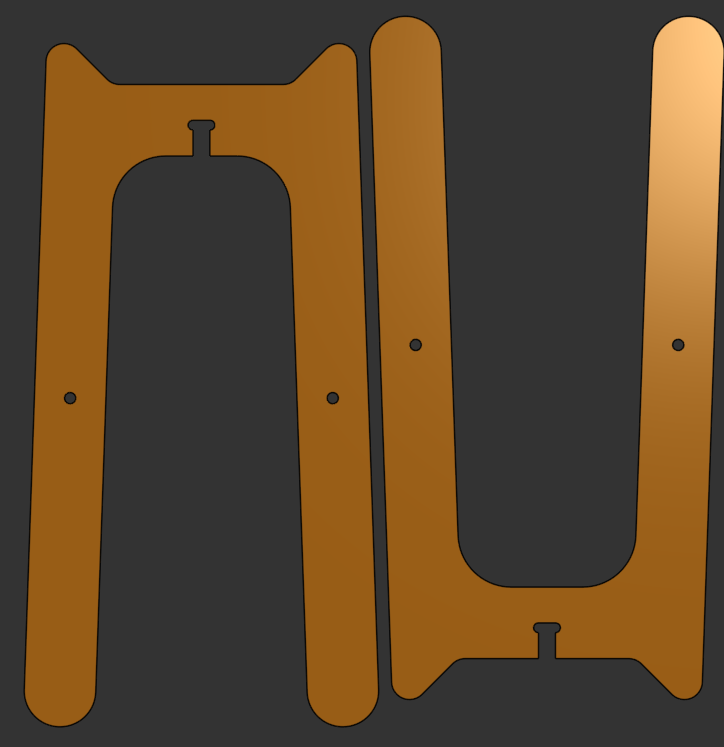
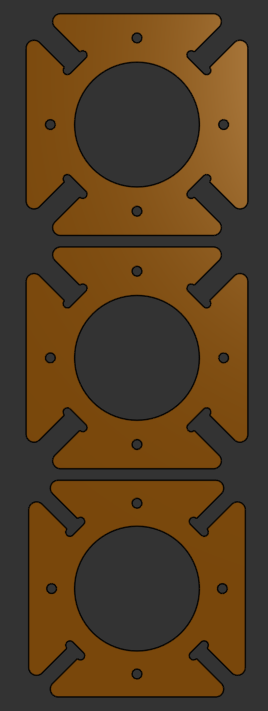
Manufacturing
At the time I manufactured these stands, I had access to two CNC routers. One was a meter by meter X-Carve, which I used for the larger stands, and the other my robotics team’s Omio x8 that I would make the rest of the parts on with its smaller bed yet finer control.
I started on the X-Carve, which I loaded a program combining a bore and contour operation. I did all of my operations in one file due to this machine not remembering its zeroes very well between operations (at least with the software we use to control it, Easel). The drawback to setting the operation up this was was that I couldn’t interrupt and edit the toolpaths I ran on it, so I ran into a couple issues. The main issue was that I had been a bit off on the y zero I set, which led to the top two stands having their tops clipped off. Thankfully my sister didn’t mind, so it ended up working out. The second issue I had is that I couldn’t do my normal procedure for securing parts, ie. running a bore operation and pausing to screw them down, so the next best option was using tabs. I don’t have too much experience using them, so I overdid it in both their size and number. I ended up using a combination of chiseling and filing the tabs, which worked but took more time than I initially intended these to take. This was definitely a learning experience, and I took a different approach to the other parts on the Omio.
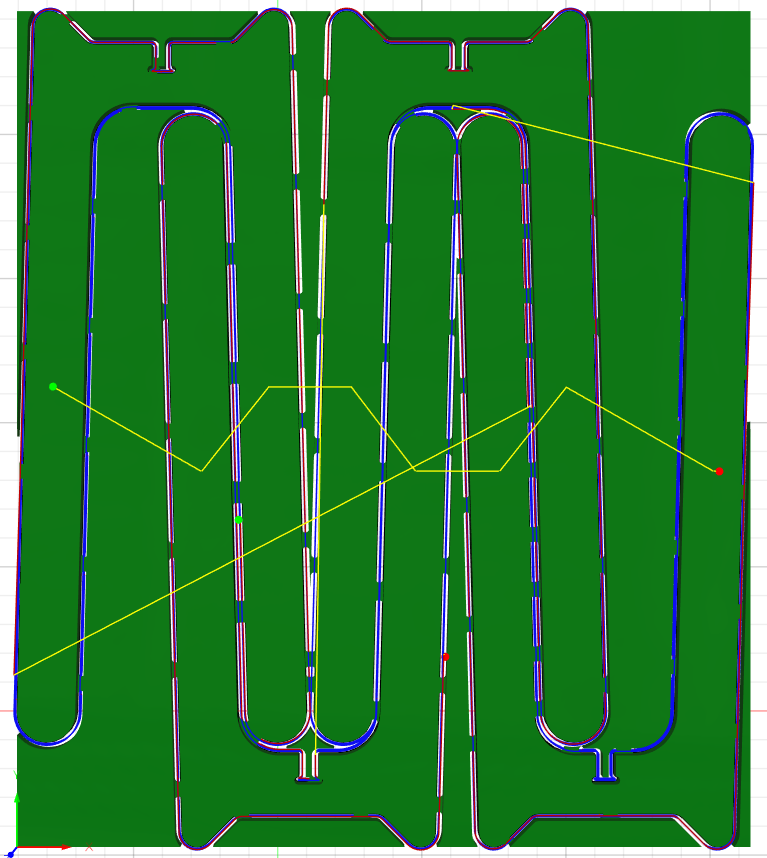
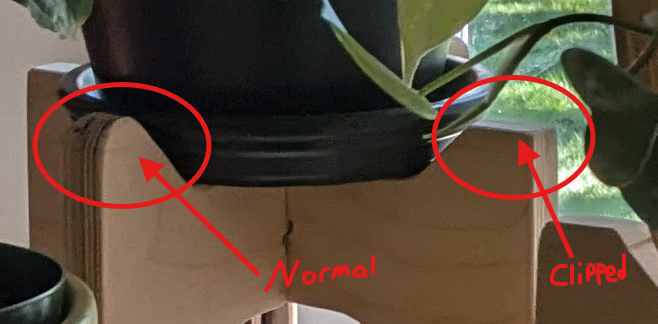
The next parts I made were for the shorter stand, which I could use multiple programs to make on the Omio. The first one I ran was a boring operation using Fusion’s drill feature, which let me add holes to the model to screw it to the wasteboard. After that and another bore operation for pre-existing holes on the model, I secured the parts and ran a normal contour without any tabs.
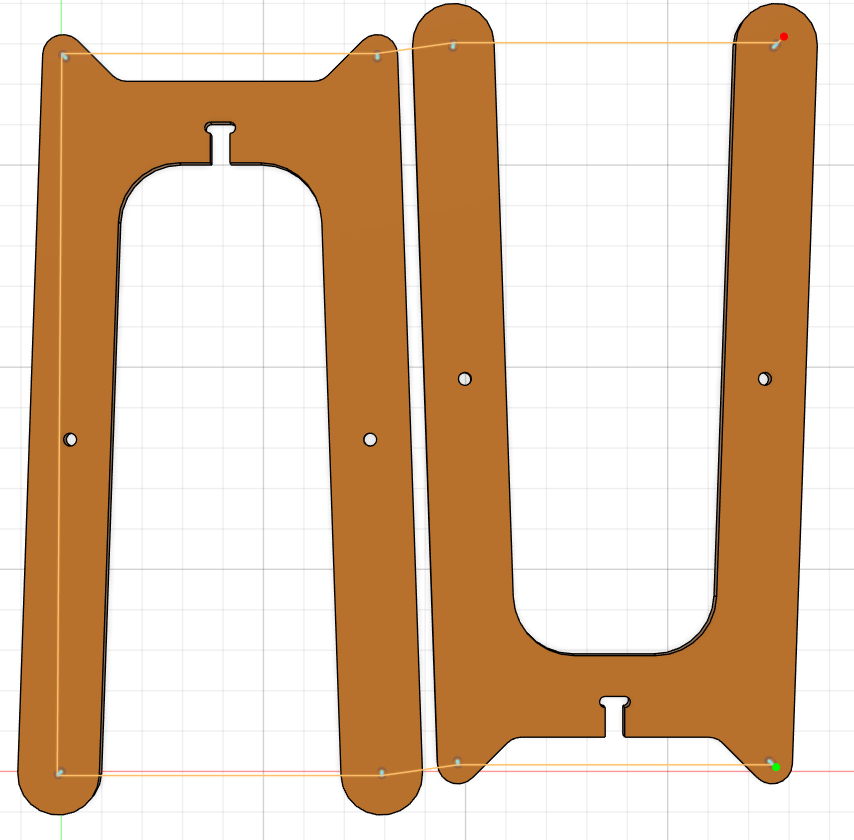
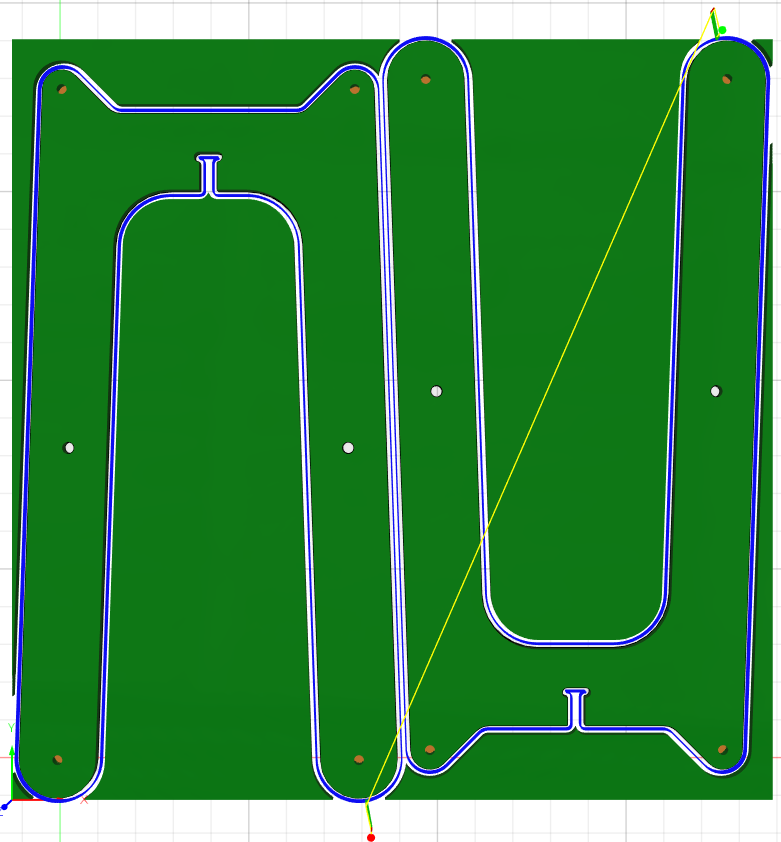
The final parts I milled were the braces, which I used scrap plywood for due to their small size. I couldn’t fit all three onto the same piece of scrap, so I ran the brace for the shorter stand with it’s own toolpaths before doing the taller braces. I started with a bore operation to create holes for securing the part, then two separate contour operations. One was a shallow ramp with tabs for cutting out the middle of the brace, while the other was a deeper, faster contour where I entered with a lead-in from outside the stock.
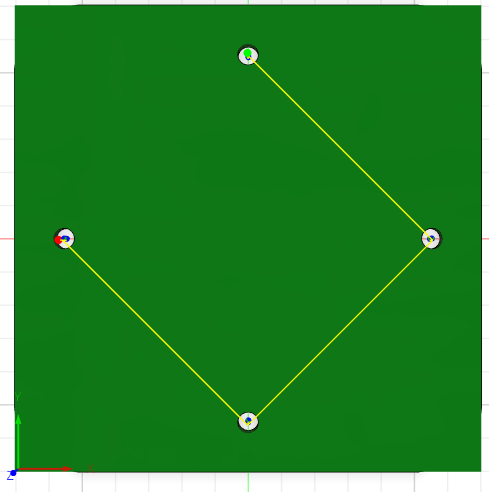
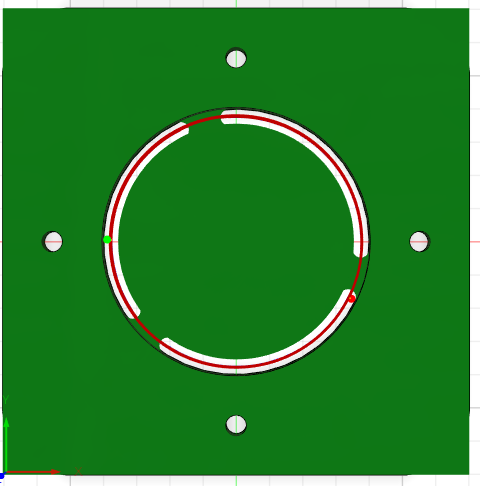
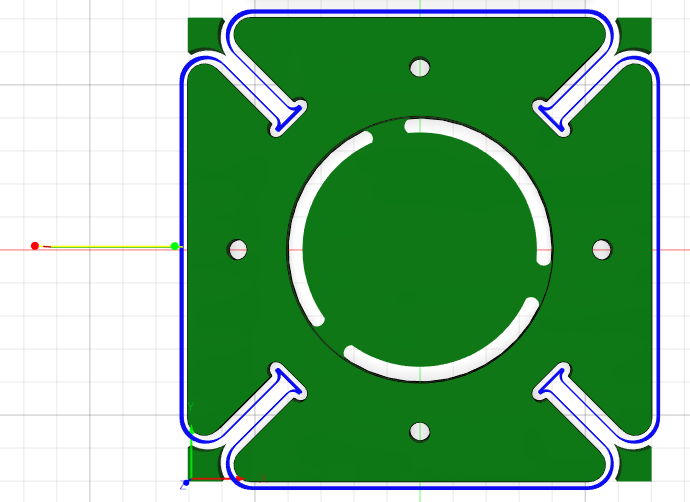
I ran pretty much the same operations with the other braces, except that I did both at once on a larger piece of stock and that I remembered how much I get annoyed at tabs. Instead of ramping down and making tabs, I manually drilled holes in the middle of the cutout and secured the center myself.
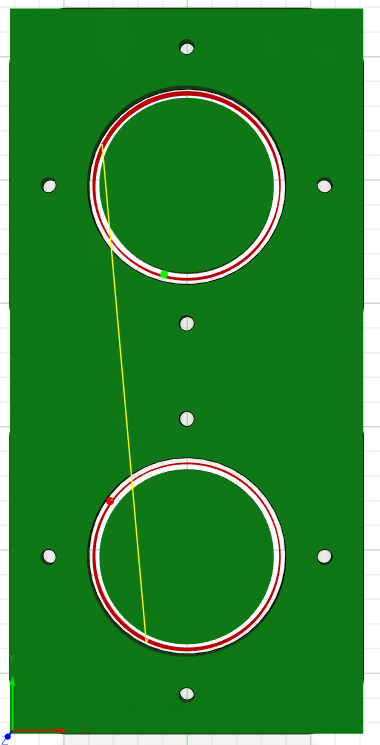
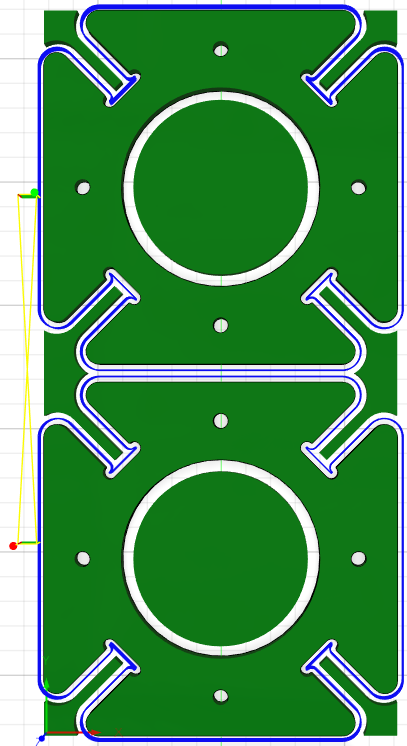
After all the parts were cut out, I spent too much time cutting off the tabs and getting rid of the live edges from the wood. I also had to do a considerable amount of sanding on all of the parts’ slots, since I wanted them all to have a tight fit and as such made them a bit tight.
In the end, they turned out all right. If I were to remake them, I’d certainly add hold-down holes to all of the parts and do away with using tabs. Additionally, I’d spend the time and effort to test the fit of the slots to reduce filing/sanding time, as well as possibly trying out a chamfer or engraving bit to debur. There are probably better ways to be material efficient than what I landed on, so I may have some experimenting to do if my sister needs more.
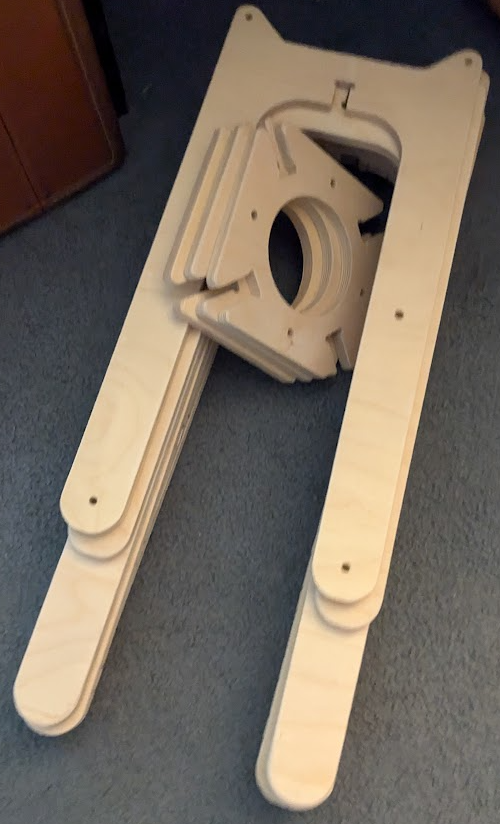
Link to CAD document – Plant Stands