It’s been a very busy senior year, and I haven’t had many opportunities to do writeups and post projects that I’ve completed or am working on. To address this (and to not look like I’m slacking on my resume and a college waitlist) I’d like to share a few details and pictures below. I know, I know, the point of this portfolio is to go into my reasoning and process but I’ve had and still have homework and studying to do. Stay tuned for the full writeups for what is below.
Dust Shoe V7, V7.1
I don’t like beating a dead horse, but I really like my Dust Shoes and keep finding room for improvement. I’ve started from close to scratch a couple times and have done enough iteration to warrant a V7 and a V7.1, which had around 25 hours of use-time and 15 hours of modification/print time in between iterations.
New features for the V7 include
- Rectangular hose-interface for more hose-end area in a limited height
- Modified body geometry to allow cover to be removed from the side rather than bottom
- Lights mounted back on the brush-mount for easier replacement
- Brush traced/cut by machines rather than by hand or with jig for easier fabrication and better accuracy.
- Compatible with V4 spindle mount, V6 spotlights
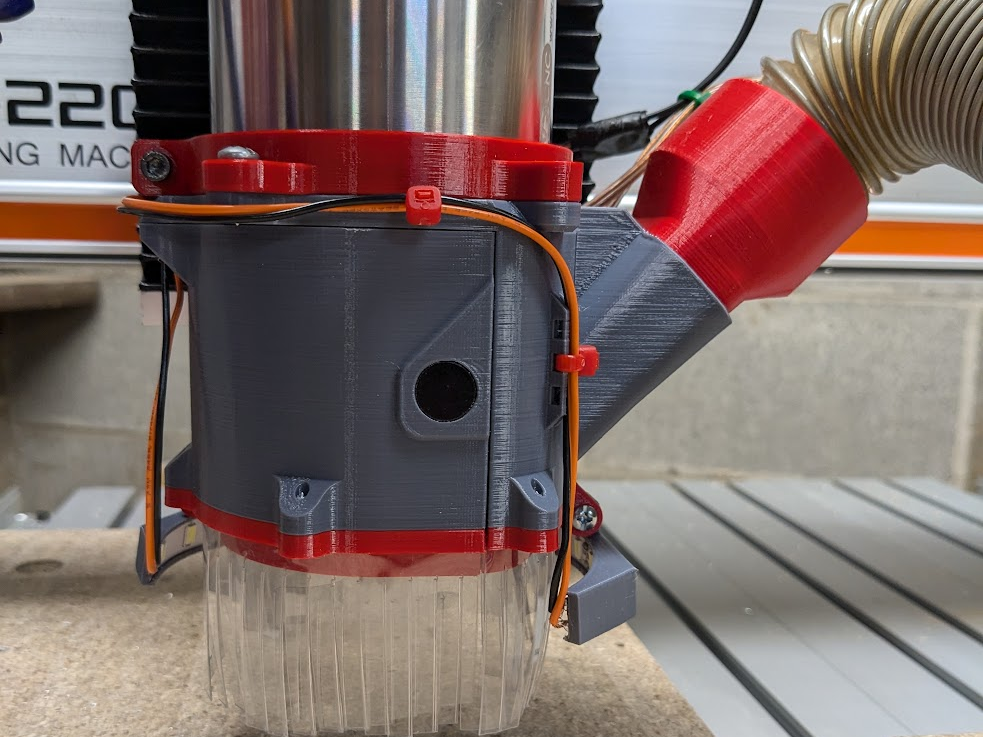
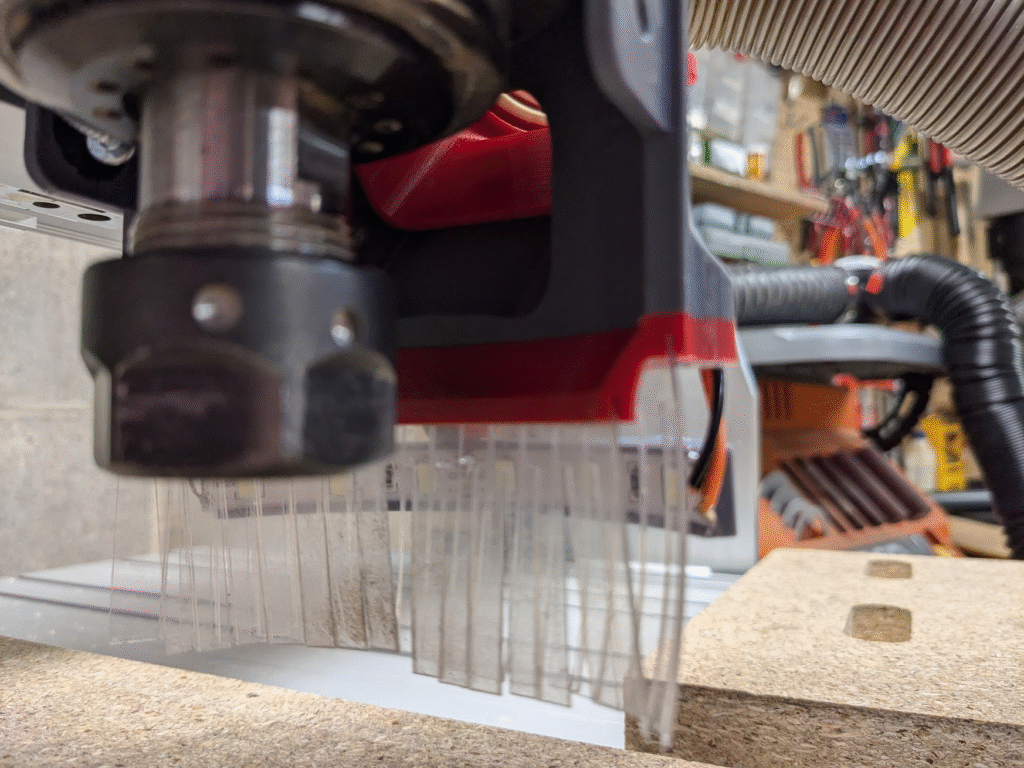
New features for the V7.1 include
- Toggle latch built into spindle mount to make adjusting height easier
- Better wire routing and ease of repair using Wagos
- WIP fix for lights flickering due to poor wire connections
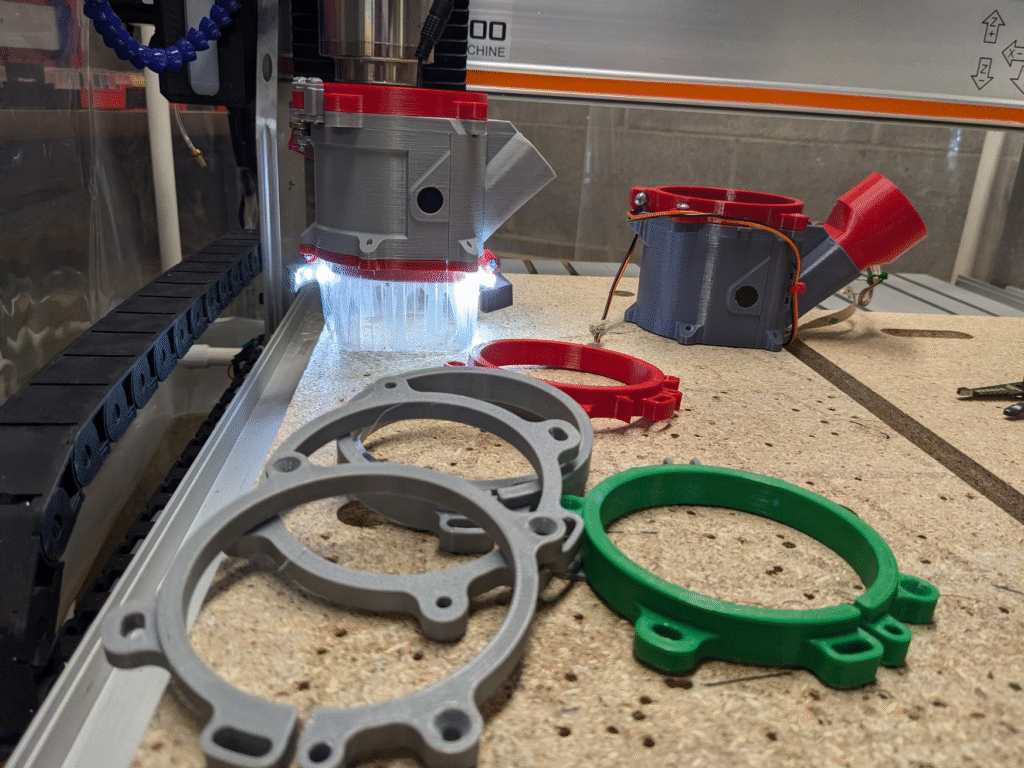
2025 FIRST Robotics Competition Robot
I’ve probably spent over a hundred hours afterschool in its basement prototyping, doing CAD, and machining for my team’s robot this year. The best part has easily been machining, which I’ve learned and improved on so much this year; it isn’t necessarily design, but it helps to know how a part will be manufactured and I’m passionate for the process.
Some things I’d like to note
- Learnt sheet metal models in Onshape, and how to design bent parts
- Learnt how to export and machine parts to bend, and methods for bending them
- Experimented more with Adaptive toolpaths and their usecases
- Minimized time spent pocketing by using full depth cuts with stepovers as much as possible
- Optimized toolpaths with aggressive but manageable feedrates and depth of cut
- Experimented with designing configurable prototypes
- Experimented with arranging parts in a modeled piece of large sheet stock
Thinking back on the season, most of what I’ve done has been prototyping and machining. I haven’t had much opportunity do design large swaths of our robot like last year, but I’m happy with my focuses this season.
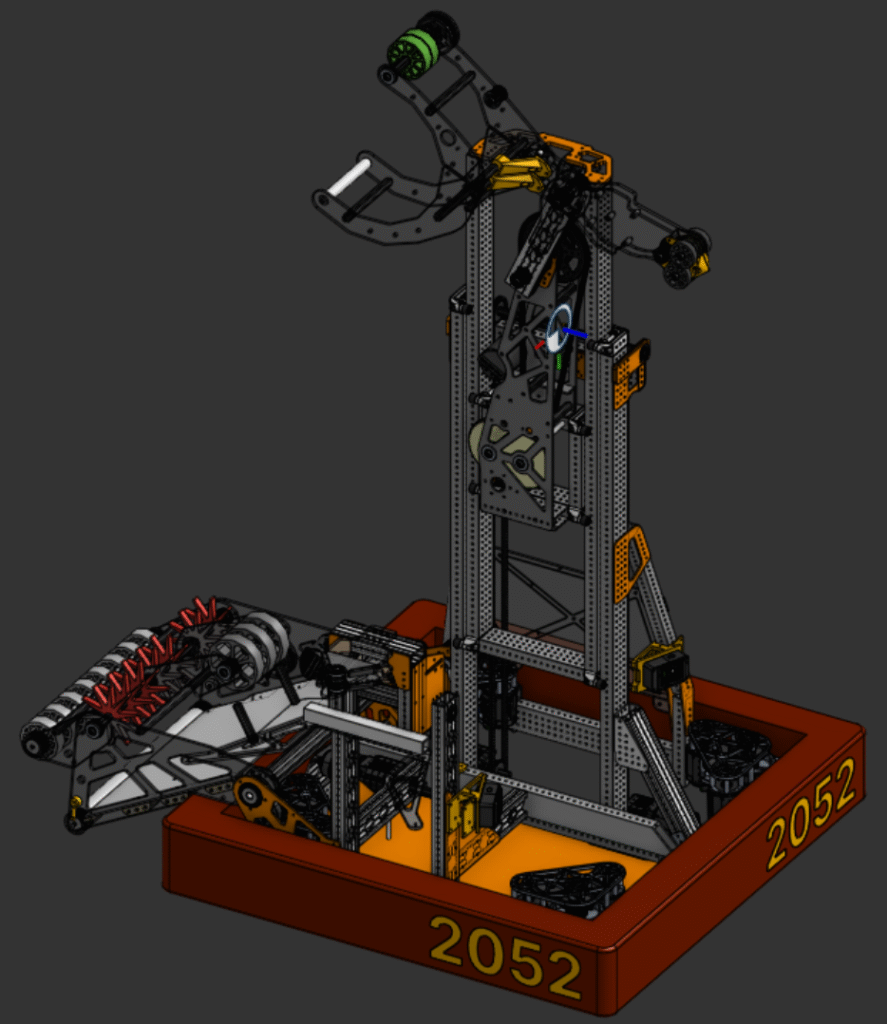
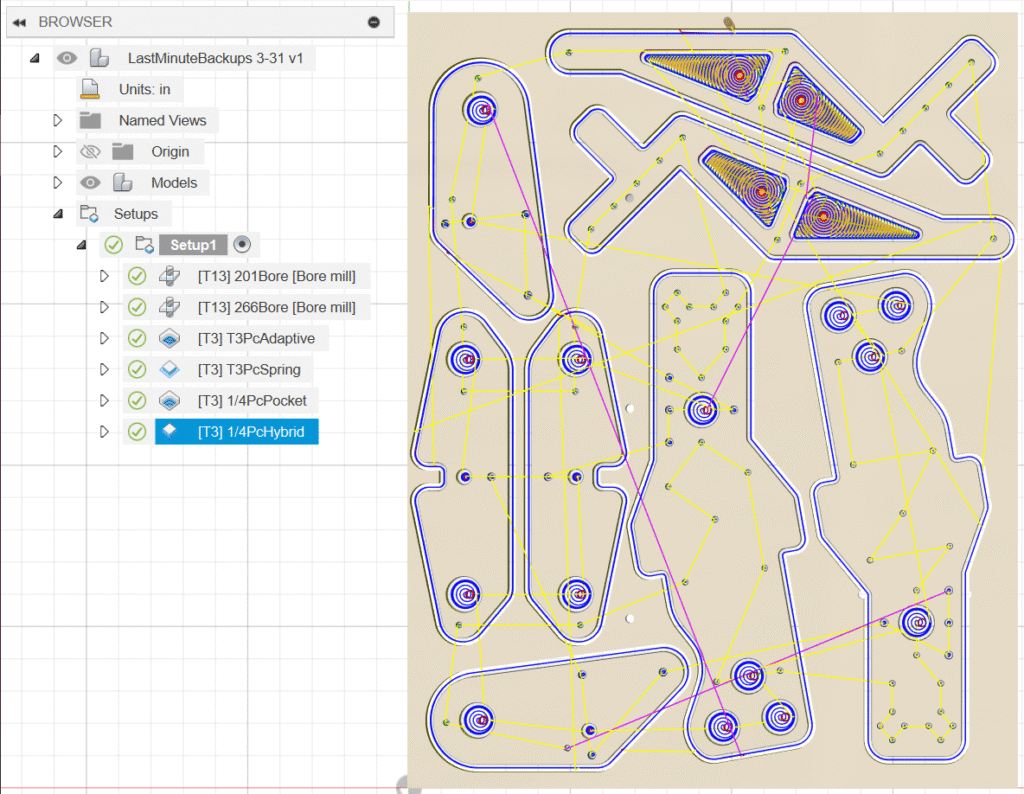
Engraved Dogtags
This was a quick and fun project where I engraved dogtags I got at a surplus store with my robotics team’s logo and some details, which I gave out to people I talked to at competitions. These were pretty simple to do, as I hogged out a piece of scrap wood with the tag’s profile and the press fit them in.
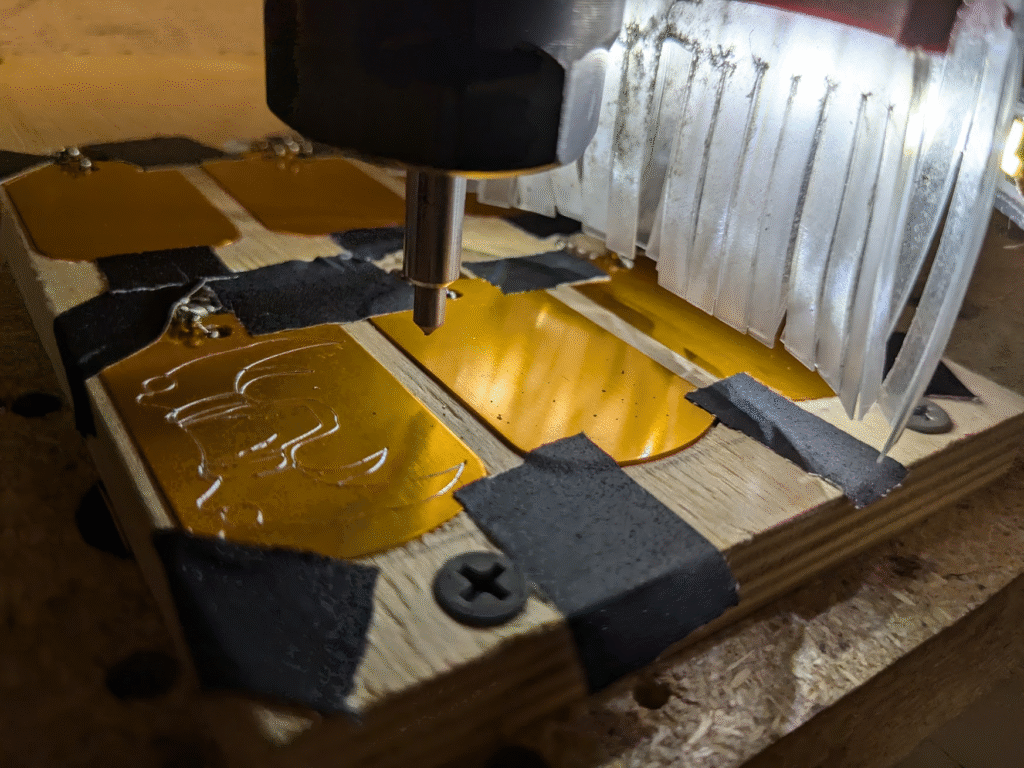
Big Vise
I made a big, more squat vice that I can leave on the CNC router as the wasteboard gets surfaced. That way I can machine the edge of its static jaw to be as parallel to the Y axis as possible and be pretty accurate. My hubris hurt me when I tried to chamfer every edge, leading to a couple holes and pockets being misaligned slightly; with a machined-flat jaw, it doesn’t cause many issues but I’ll elaborate more in a later writeup.
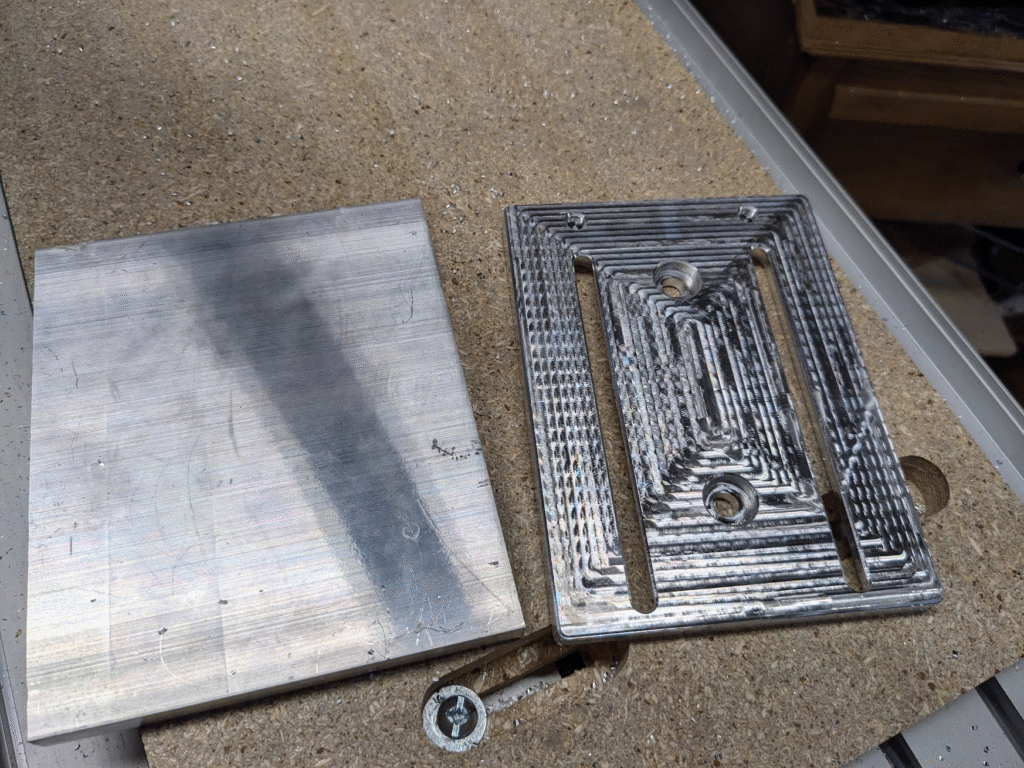
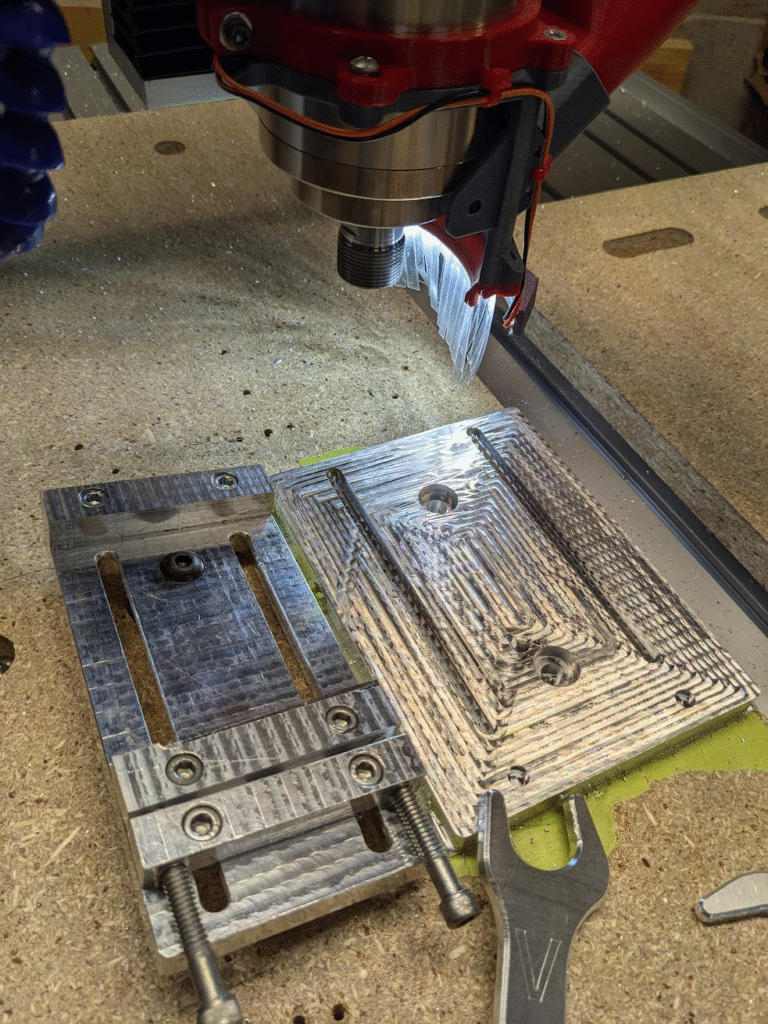
Long, Engraved Collet Wrenches
I don’t know if I’ll add a whole new writeup about these since I used the same process as with the decorative wrenches from an earlier post, but these warrant at least a mention.
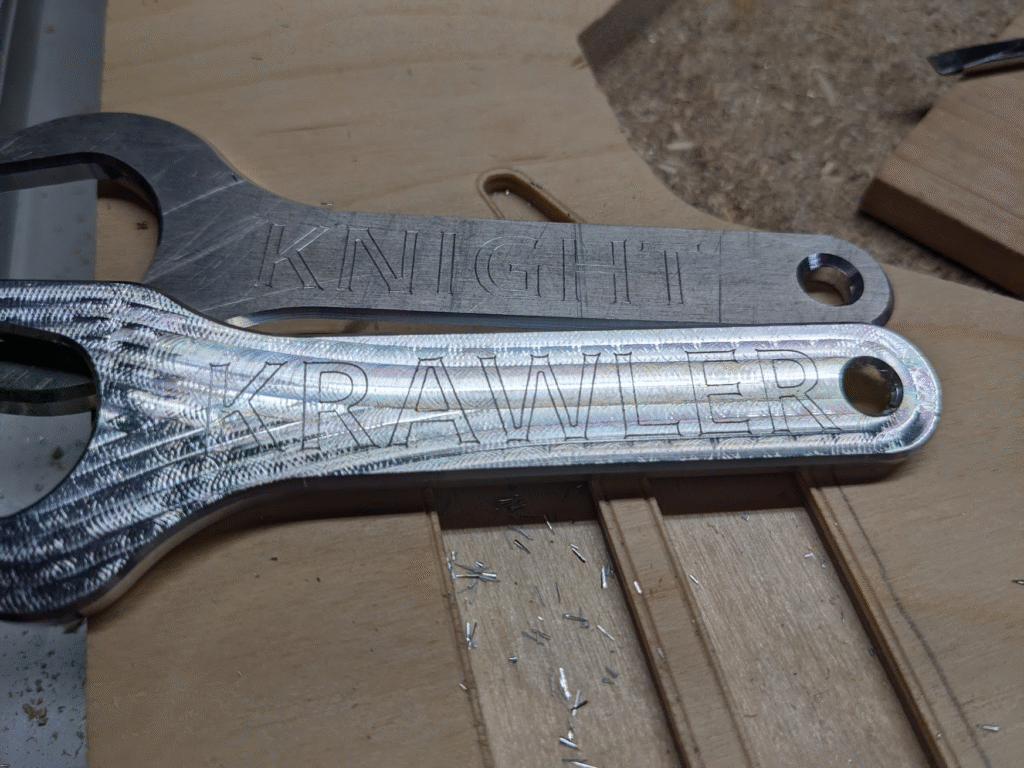
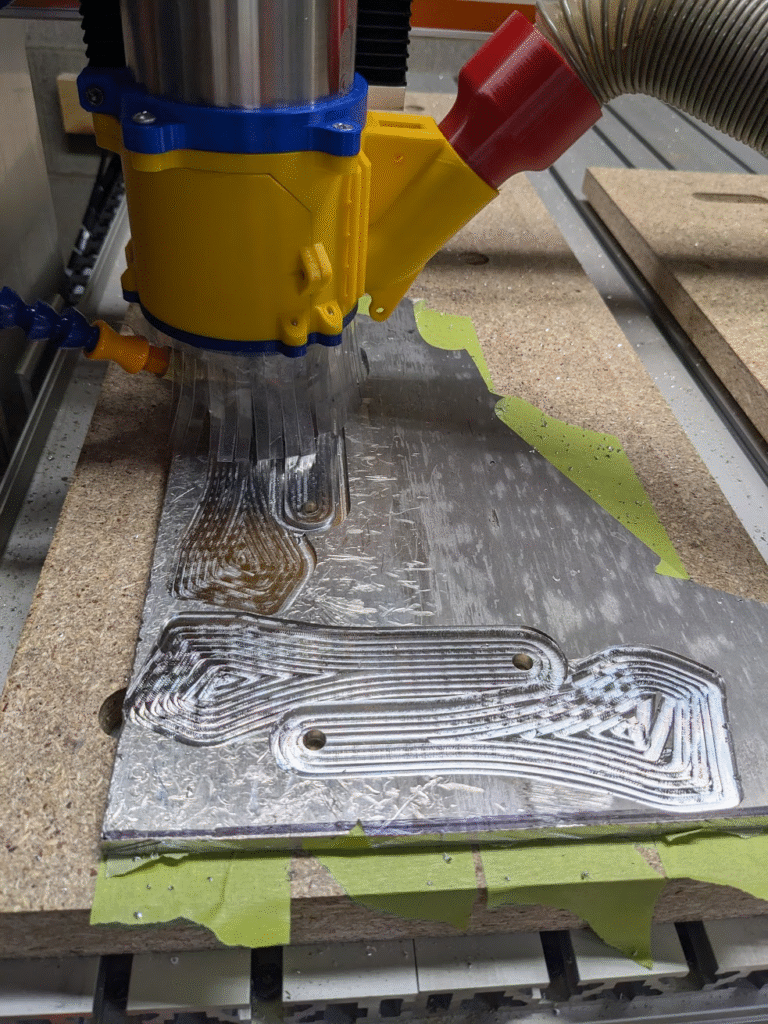
Custom Rockstop
I’m working on a gift for my music teacher of the last 4 years, and I figured I’d machine something that she could use. Also, a bit of vocabulary; a rockstop is an accessory for cellos and sometimes double basses to protect floors from their metal endpins that act as a third point of contact with the floor and to prevent the endpin from dramatically shifting position on the floor, potentially dropping a multi-thousand dollar musical instrument.
Some things I’d like to note
- WIP, I’ve made only a couple plastic prototypes so far of one component to visualize and test it
- Various TPU 3D-Printed ‘stoppers’ on bottom to test what will prevent sliding the best
- I’m trying to design it to accommodate both friction-based and tension based use – the two types of rockstop I’ve used have either attached via strap to a chair or stayed in place via friction. There are pros to both types, and I’d like to make this one work as both
- I’ve tried to be as accurate as I can and get the best finishes I can on this project, challenging myself to stay within 5 thou of nominal and changing my machining strategies as I do so
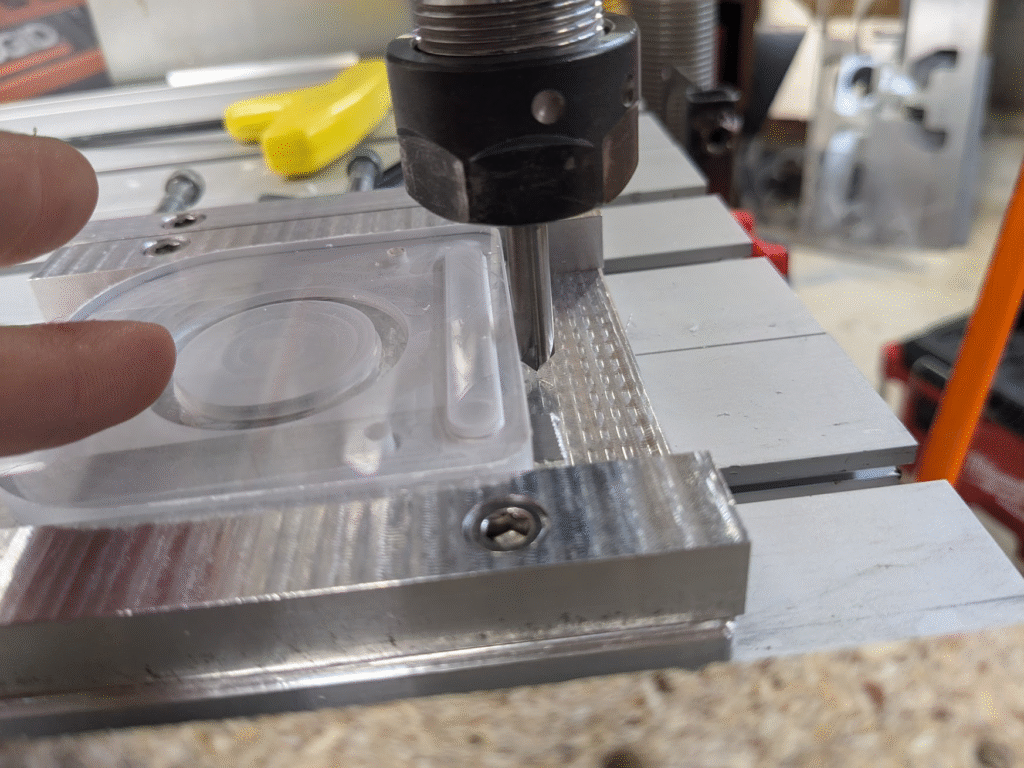
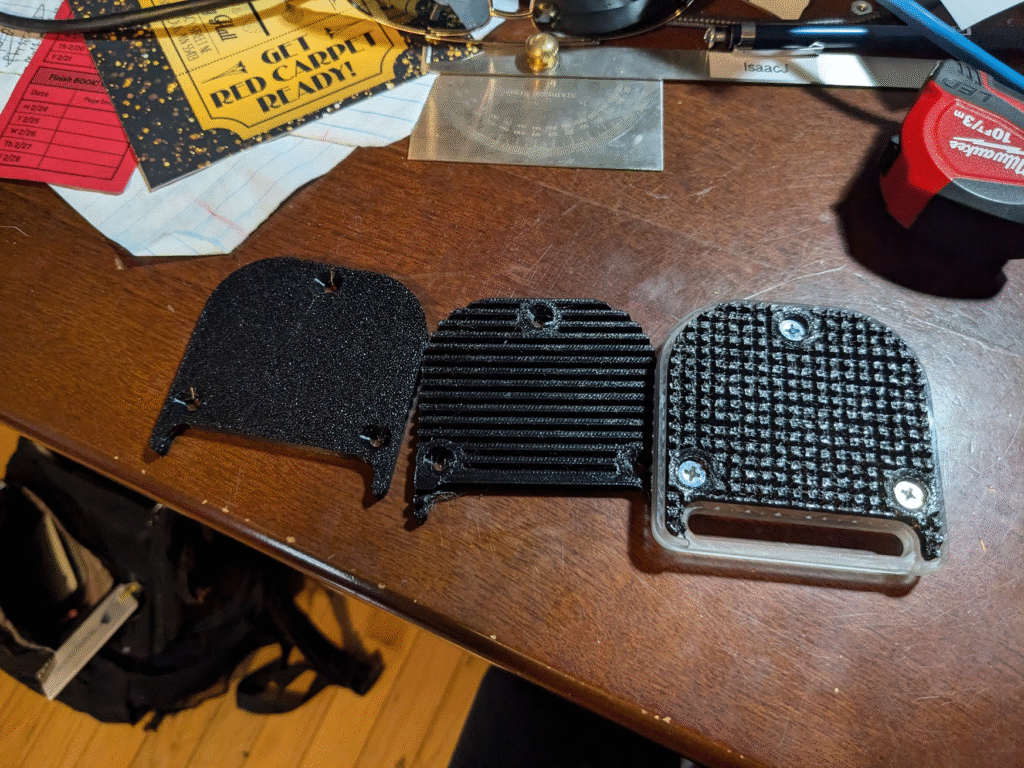

Leave a Reply